Band hose clamps reusable-Versatility and Efficiency in Fluid Systems
Reusable band hose clamps are essential components in a wide range of applications, from automotive to industrial settings, where secure…
Reusable band hose clamps are essential components in a wide range of applications, from automotive to industrial settings, where secure and leak-free connections are critical. These clamps offer a reliable and adjustable solution to hose and pipe connections, ensuring safety and efficiency. This article explores the design, application, and benefits of reusable band hose clamps, highlighting their importance in maintaining the integrity of fluid systems.
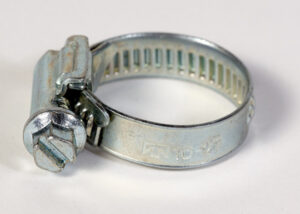
Design and Functionality
Reusable band hose clamps are designed to provide a secure and adjustable connection between hoses and fittings. The primary components of these clamps include a band, a nut, and a bolt。 The band is typically made from metal, such as stainless steel, which offers corrosion resistance and durability. The nut and bolt work together to apply radial pressure, ensuring a tight seal and preventing fluid leakage.
One of the key advantages of reusable band hose clamps is their ability to be easily removed and reapplied without losing their effectiveness. This feature is particularly useful in situations where hoses need to be frequently disconnected or replaced, such as in maintenance or repair work。
Applications and Benefits
Reusable band hose clamps are widely used in various industries due to their versatility and reliability. They are commonly found in automotive applications, industrial pipelines, and even in residential settings where hoses need to be securely attached to fittings。 The clamps provide uniform pressure around the hose, ensuring a strong seal and preventing leaks。
The use of reusable band hose clamps enhances hygiene, safety, and efficiency while adhering to strict regulatory standards in industries such as food and beverage。 In these environments, the ability to quickly and easily disconnect and reconnect hoses without compromising the seal is crucial.
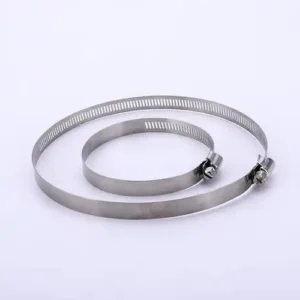
Advantages Over Traditional Clamps
Reusable band hose clamps offer several advantages over traditional hose clamps. One significant improvement is the use of solid, embossed thread bands instead of perforated bands found in conventional designs。 This solid construction eliminates the弱点 of perforations that can lead to micro-cracking and crevice corrosion, which are common failure points in traditional clamps。
Additionally, reusable band hose clamps often feature interlocking mechanisms rather than folded and spot-welded bands, which further reduces the risk of water entrapment and corrosion。 This design improvement makes them well-suited for wet locations and applications where traditional clamps may fail.
Installation and Maintenance
Proper installation is crucial for the effectiveness of reusable band hose clamps. It is essential to select the correct clamp size for the hose and fitting diameter and to ensure that the hose is fully seated on the fitting before applying the clamp。 The clamp should be positioned evenly around the circumference of the hose and tightened gradually to avoid over-tightening。
Regular maintenance and inspection of reusable band hose clamps are also important to ensure their continued performance and to prevent failures. This includes cleaning the clamps and surrounding areas to remove debris and corrosive materials, as well as replacing clamps that show signs of significant wear or damage。
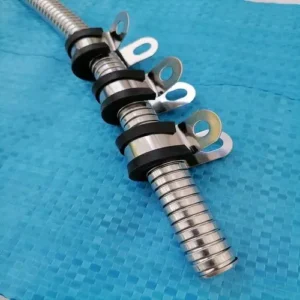
Reusable band hose clamps provide a reliable and efficient solution for securing hoses in various applications. Their design improvements over traditional clamps, such as solid thread bands and interlocking mechanisms, offer greater resistance to corrosion and failure. By ensuring proper installation and regular maintenance, these clamps contribute to the safety, efficiency, and reliability of fluid systems in industries ranging from automotive to food processing.
Problems and Solutions
1. Sealing problem
Problem description: After the pipe clamp is installed, leakage occurs at the connection, resulting in a drop in fluid system pressure, reduced efficiency, and even possible fluid waste or equipment damage.
Solution
Check the installation: Make sure that the pipe clamp is installed in the correct position, fits tightly on the hose, and the tightening force is uniform and moderate. If the installation is too loose, the pipe clamp position should be readjusted and tightened appropriately; if it is too tight, the hose may be damaged and it needs to be loosened appropriately before reinstalling.
Replace the gasket: If the gasket is aged, damaged or deformed, it should be replaced with a new gasket in time. Choose a high-quality gasket that matches the pipe clamp and hose to ensure good sealing performance.
Clean the surface: Before installing the pipe clamp, thoroughly clean the surface of the hose and connecting parts to remove oil, dust and impurities to avoid affecting the sealing effect.
2. Hose damage problem
Problem description: The pipe clamp may cause damage such as extrusion, wear or cutting to the hose during use, shortening the service life of the hose, or even causing the hose to rupture and cause fluid leakage.
Solution
Choose a suitable pipe clamp: Choose a pipe clamp of appropriate specifications based on the material, outer diameter and working pressure of the hose. Avoid using too large or too small pipe clamps, and ensure that the pipe clamps and hoses match well.
Adjust the installation method: When installing the pipe clamps, be careful to avoid the edges or screws of the pipe clamps directly contacting the hose surface. You can add protective pads or use appropriate installation tools at the contact point to apply pressure evenly to prevent local excessive extrusion.
Regular inspection: Check the pipe clamps and hoses regularly to detect and deal with hose damage in a timely manner. For minor damage, repair measures such as bandaging protection can be taken; for severely damaged hoses, they should be replaced in time.

3. Loose pipe clamp problem
Problem description: During the operation of the fluid system, due to vibration, pressure fluctuations and other reasons, the pipe clamps may become loose, affecting the stability and sealing of the connection.
Solution
Add anti-loosening measures: Auxiliary tools such as anti-loosening nuts, spring washers or thread lockers can be used to prevent the pipe clamps from loosening. When installing nuts, ensure that the tightening torque meets the requirements and mark them if necessary for subsequent inspection.
Strengthen fixation: For parts with large vibration, the fixing effect of the pipe clamp can be strengthened by increasing the number of pipe clamps, using double clamps or installing fixed brackets to reduce the impact of vibration on the pipe clamp.
Regular inspection and maintenance: Establish a regular inspection system to promptly detect the looseness of the pipe clamp and tighten it. During system maintenance, all pipe clamps should be fully inspected and tightened to ensure that they are in good working condition.
4. Corrosion problem
Problem description: If the pipe clamp is in a corrosive environment such as moisture, acid and alkali for a long time, corrosion may occur, resulting in reduced strength of the pipe clamp, affecting its service life and sealing performance.
Solution
Select corrosion-resistant materials: According to the working environment of the fluid system, select pipe clamp materials with good corrosion resistance, such as stainless steel, galvanized steel or plastic. For harsh corrosive environments, pipe clamps with special anti-corrosion coatings or coating materials can be selected.
Protective treatment: Perform surface protective treatment on the pipe clamp, such as painting, galvanizing, spraying, etc., to improve its corrosion resistance. When installing the pipe clamp, avoid direct contact with corrosive substances, and take isolation measures if necessary.
Regular replacement: For pipe clamps used in corrosive environments for a long time, they should be replaced regularly according to their degree of corrosion and service life to ensure the safe and reliable operation of the fluid system.
5. Compatibility issues
Problem description: In some complex fluid systems, pipe clamps may not match other components, such as slight differences in pipe diameters, incompatible connection methods, etc., resulting in difficult installation or loose connections.
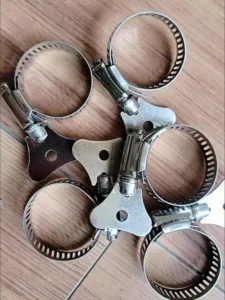
Solutions
Accurate measurement and selection: Before purchasing pipe clamps, accurately measure the outer diameter of the hose, the size of the connecting parts, etc., to ensure that the specifications of the selected pipe clamps are completely matched with the actual size. At the same time, it is necessary to fully understand the connection requirements of other components in the system and select the appropriate pipe clamp model.
Use conversion joints: If there are differences in connection methods or sizes between the pipe clamps and existing components, you can consider using conversion joints to achieve compatibility. Select a suitable conversion joint to ensure that it is reliably connected to the pipe clamps and other components, and pay attention to the sealing performance.
Customized solutions: For special compatibility issues, you can communicate with suppliers or manufacturers to seek customized solutions. Design and produce special pipe clamps or connecting parts according to actual needs to ensure that they are perfectly compatible with the entire fluid system.