Heavy Duty Hose Clamps: The Backbone of Industrial Fluid Transfer
In the world of industrial applications, where high-pressure fluid transfer is a common requirement, heavy duty hose clamps play a…
In the world of industrial applications, where high-pressure fluid transfer is a common requirement, heavy duty hose clamps play a pivotal role in ensuring the integrity and safety of fluid systems. These clamps are designed to withstand extreme conditions and provide a secure, leak-proof connection between hoses and fittings. This article will explore the importance of heavy duty hose clamps, their applications, types, and the factors to consider when selecting the right clamp for your specific needs.
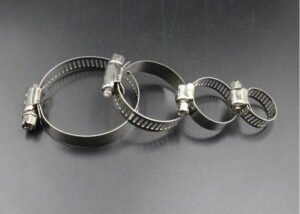
The Importance of Heavy Duty Hose Clamps
Heavy duty hose clamps are critical for maintaining the efficiency and safety of fluid transfer systems in industries such as construction, automotive, marine, and industrial machinery. They serve several vital functions:
1.Leak Prevention: Clamps prevent fluid leaks, which can lead to system failures, environmental damage, and safety hazards.
2.Pressure Resistance: They are designed to withstand high pressures, ensuring that hoses do not burst or detach under stress.
3.Durability: Made from robust materials, these clamps can endure harsh environments and resist corrosion and wear.
4.Ease of Installation: Many heavy duty hose clamps are easy to install and remove, facilitating maintenance and repair.
Applications of Heavy Duty Hose Clamps
1.Hydraulic Systems: In construction and heavy machinery, hydraulic systems rely on hose clamps to maintain pressure and prevent leaks.
2.Pneumatic Systems: Industrial automation often uses pneumatic systems, and hose clamps are crucial for secure air line connections.
3.Marine Applications: On ships and boats, clamps are used to secure hoses carrying fuel, oil, and water, ensuring safety and compliance with maritime regulations.
4.Automotive: In vehicles, especially those involved in off-roading or heavy-duty work, hose clamps are essential for maintaining the integrity of the cooling and fuel systems.

Types of Heavy Duty Hose Clamps
There are several types of heavy duty hose clamps, each with its own advantages and suitable applications:
1.Band Clamps: These are the most common type, featuring a metal band that tightens around the hose with the help of a screw or bolt.
2.Wing Nut Clamps: Similar to band clamps but use a wing nut for tightening, providing a quick-release option.
3.Ear Clamps: These clamps have lugs or ears that can be bolted together, providing a strong and secure connection.
4.Push-On Clamps: These clamps are pushed onto the hose and provide a quick and easy connection, though they may not be as secure as other types.
5.Pinch Clamps: Also known as worm drive clamps, these clamps offer a high level of security with their worm gear mechanism.
Factors to Consider When Selecting Heavy Duty Hose Clamps
When choosing the right heavy duty hose clamp, consider the following factors:
1.Hose Material: The clamp must be compatible with the material of the hose to avoid damage or leakage.
2.Hose Diameter: Clamps are available in various sizes to fit different hose diameters.
3.Working Pressure: The clamp must be rated for the pressure of the fluid system it will be used in.
4.Temperature Range: The clamp material should be able to withstand the temperature range of the fluid being transferred.
5.Corrosion Resistance: For applications involving corrosive fluids, choose clamps made from corrosion-resistant materials.
6.Ease of Use: Consider the convenience of installation and removal, especially in hard-to-reach areas.
Heavy duty hose clamps are indispensable in maintaining the safety and efficiency of fluid transfer systems in various industries. By understanding the importance of these clamps, their applications, types, and the factors involved in their selection, one can ensure that the right clamp is used for each specific application. This not only prevents potential hazards but also optimizes the performance of the systems in which they are used. As with any critical component, regular maintenance and inspection of hose clamps are essential to prevent failures and extend the life of the fluid transfer systems they secure.

Possible problems
1.Leakage due to poor sealing
Cause Analysis
Uneven hose surface: If the hose surface has scratches, bumps or depressions, it may not form a good seal when clamped with a pipe clamp. For example, in an industrial environment that transports chemically corrosive liquids, the hose may be corroded by chemicals, causing surface damage.
Improper pipe clamp selection: It is a common problem that the size of the pipe clamp does not match the hose. If the diameter of the pipe clamp is too large, it is difficult to provide enough pressure to seal the hose even if it is tightened; if the diameter of the pipe clamp is too small, it may damage the hose and it will not be able to seal effectively.
Improper installation: Failure to tighten the pipe clamp evenly during installation or failure to place the pipe clamp in the correct position may result in poor sealing. For example, the fastening bolts of the pipe clamp are not tightened symmetrically, making the pressure of the pipe clamp on the hose uneven.
Solution
For the case of uneven hose surface, the hose surface should be checked and repaired first. If the scratch is shallow, it can be smoothed with sandpaper; if the damage is more serious, the hose needs to be replaced. At the same time, before installing the pipe clamp, make sure the hose is clean and free of debris.
Correct selection is the key. Before installing the pipe clamp, accurately measure the outer diameter of the hose and select the appropriate size of the pipe clamp according to the outer diameter. Generally speaking, the inner diameter of the pipe clamp should be slightly smaller than the outer diameter of the hose to ensure a good clamping effect.
During installation, use appropriate tools (such as a torque wrench) to evenly tighten the fastening bolts of the pipe clamp according to the specified torque value. And make sure that the pipe clamp is installed in the correct position, usually close to the hose connection to enhance the sealing effect.
2.Insufficient pipe clamp strength leads to damage
Cause Analysis
Poor material quality: If the pipe clamp is made of low-quality metal material, its strength and toughness may not meet the requirements of industrial fluid transportation. For example, when conveying high-pressure and high-temperature fluids, poor-quality pipe clamps may deform or break.
Overload: When the fluid pressure exceeds the rated pressure of the pipe clamp, or additional external force is applied to the pipe clamp (such as collision with other equipment), the pipe clamp may be damaged.
Solution
To select reliable quality pipe clamps, check the material composition and quality certification of the pipe clamps. For example, for high-pressure and high-temperature fluid delivery applications, pipe clamps made of high-strength materials such as stainless steel can be selected, which have good corrosion resistance and mechanical properties.
During the installation process, the working environment of the pipe clamp and the maximum pressure it may withstand should be considered. When designing a fluid delivery system, the fluid pressure should be accurately calculated and pipe clamps with a rated pressure higher than the actual working pressure should be selected. At the same time, the pipe clamps should be properly protected to avoid accidental damage such as external collisions.

3.Pipe clamps rust and corrode
Cause Analysis
Working environment factors: If the pipe clamp is in a humid environment with corrosive gases or chemicals, it is easy to rust and corrode. For example, in industrial facilities near the sea, the high salt content in the air can easily cause the metal parts of the pipe clamp to rust.
Material compatibility issues: Corrosion can also occur if the pipe clamp material is incompatible with the fluid being transported. For example, when transporting acidic liquids, pipe clamps made of ordinary carbon steel may be corroded by the acid.
Solution
For harsh working environments, the pipe clamps can be surface treated, such as galvanizing, painting and other anti-corrosion treatments. Check the surface condition of the pipe clamps regularly. If rust is found, clean it in time and re-treat it with anti-corrosion.
Choose pipe clamp materials that are compatible with the fluid and working environment. For example, when conveying corrosive liquids, pipe clamps made of plastic or corrosion-resistant alloys can be selected. At the same time, in the design and selection process of pipe clamps, environmental factors should be considered and the requirements for anti-corrosion measures should be appropriately increased.