How to make a hose clamp out of wire
In various DIY projects and emergency situations, having the ability to create a hose clamp using wire can be incredibly…
In various DIY projects and emergency situations, having the ability to create a hose clamp using wire can be incredibly useful. Hose clamps are essential for securing hoses and preventing leaks, especially in automotive and plumbing applications. This guide will walk you through the process of making a hose clamp out of wire, which can be a temporary or even a permanent solution depending on your needs.
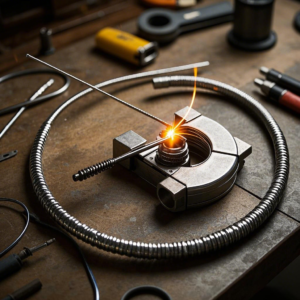
A hose clamp, also known as a hose clip or worm drive clamp, is a device used to secure hoses to fittings or other components. Traditional hose clamps are made from metal and have a screw mechanism to tighten the clamp. However, in the absence of a store-bought clamp, a wire clamp can serve the same purpose. This article will provide a detailed tutorial on how to create a functional hose clamp using wire.
Materials Needed
1.Wire: Choose a strong, flexible wire. The thickness of the wire will depend on the size of the hose you need to clamp. A common choice is 14-gauge wire, which is strong and flexible enough for most applications.
2.Pliers: To bend and shape the wire.
3.Cutting Tool: To cut the wire to the desired length.
4.Hose: The hose you want to secure.
5.Fitting or Component: The part to which you will attach the hose.
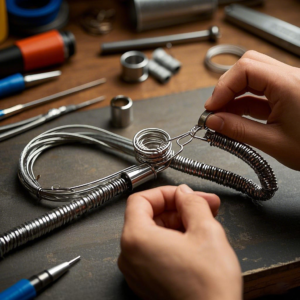
Step 1: Measure and Cut the Wire
The first step is to measure the length of wire you will need. The wire should be long enough to wrap around the hose and the fitting several times, with some extra length to form the clamp’s screw mechanism. As a general rule, you will need about 6 inches of wire for every inch of hose diameter.
1.Measure the circumference of the hose where it will be clamped.
2.Multiply this measurement by 3 to 4 to account for the wraps around the hose and fitting, and to allow for the screw mechanism.
3.Cut the wire to the calculated length.
Step 2: Shape the Wire
Now that you have the wire, you need to shape it into a form that will hold the hose securely.
1.Create a loop at one end of the wire. This loop will be used to secure the wire after it has been wrapped around the hose.
2.Bend the wire into a spiral shape, leaving enough length at the end to create the screw mechanism.
Step 3: Wrap the Wire Around the Hose
The next step is to wrap the wire around the hose to create a secure fit.
1.Start by placing the loop end of the wire around the hose and fitting.
2.Wrap the wire tightly around the hose, ensuring that each turn is close to the previous one to create a firm grip.
3.Continue wrapping until you have used about two-thirds of the wire’s length.
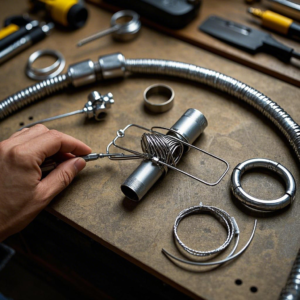
Step 4: Create the Screw Mechanism
The screw mechanism is what allows you to tighten the clamp and adjust its pressure on the hose.
1.Take the remaining wire and bend it into a spiral or a series of loops.
2.Insert the end of the wire through the first loop you created at the beginning of the wire.
3.Twist the wire to tighten the clamp. The spiral or loops will act as a ratchet, allowing you to tighten the clamp but not loosen it without unwinding the wire.
Step 5: Secure the Clamp
Once the clamp is tightened to your satisfaction, you need to secure it to prevent it from loosening.
1.Twist the end of the wire around the last loop or turn of the wire to lock it in place.
2.Use pliers to crimp the end of the wire, ensuring it cannot unravel.
Step 6: Test the Clamp
Before relying on your wire clamp, it’s important to test its effectiveness.
1.Apply pressure to the hose to simulate the conditions it will be under.
2.Check for any leaks or signs that the clamp is not holding the hose securely.
3.If necessary, adjust the tightness of the clamp by unwinding and rewrapping the wire.
Maintenance and Considerations
While a wire clamp can be a quick and effective solution, it’s not as durable as a traditional metal clamp. Here are some considerations:
1.Corrosion: Wire clamps can corrode over time, especially if exposed to moisture. Regularly inspect and replace wire clamps as needed.
2.Strength: Wire clamps may not be as strong as metal ones, particularly under high pressure. Use them for low-pressure applications or as a temporary fix.
3.Adjustability: Unlike some metal clamps, wire clamps cannot be easily adjusted once secured. If you need to adjust the tightness, you may need to remake the clamp.

Creating a hose clamp out of wire is a practical skill that can save you in a pinch. It requires basic tools and materials, and with a bit of practice, you can create a secure and effective clamp. Remember, while a wire clamp can be a temporary solution, it’s always best to use proper hose clamps for long-term, high-pressure applications. With this guide, you’re now equipped to handle hose clamping emergencies with confidence.
Problems encountered:
The hose diameter is not measured accurately, resulting in the wire clamp being too large or too small, and the hose cannot be tightly fixed.
When bending the wire, the bending angle is not accurate and round, which affects the fit and stability of the wire clamp.
When twisting the end of the wire to fix it, the strength is not well controlled, either too loose and easy to loosen, or too tight and the wire breaks.
Solution:
Use a soft ruler to measure the hose diameter several times, take the average value, ensure accuracy, and determine the required wire length.
Use pliers and other tools to assist in bending the wire, and slowly adjust the angle. You can draw a circular template on paper in advance for comparison.
When twisting the end, add force a little bit, check the tightness while twisting, and slow down the action when it is almost right to avoid excessive force.