Learn more about various types of clamps-Seikou
In modern industrial production and daily life, fixtures play a vital but often overlooked role. From precision machining workshops to…
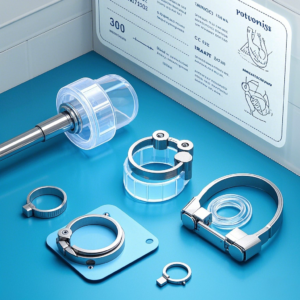
In modern industrial production and daily life, fixtures play a vital but often overlooked role. From precision machining workshops to handmade corners at home, fixtures are everywhere. With their unique functions and structures, they ensure the smooth progress of various operations. Today, let us take a deeper look at various fixtures and unveil their mysterious veil.
1. Clamp-type fixture: simple and direct power
Clamp-type fixtures are the most common and easy to understand type. They usually consist of a handle, a pivot and a jaw, and the jaw is opened and closed by operating the handle. We often see it in mechanical maintenance. For example, when replacing auto parts, the clamp-type fixture can easily fix bolts or nuts, making it convenient for maintenance personnel to disassemble and install. Its principle is based on the principle of lever. By applying a small force on the handle, a large clamping force can be generated at the jaw. This type of fixture is simple to operate and low in cost. It is widely used in various scenarios where objects need to be temporarily fixed or grasped.
2. Chuck-type fixture: Stable guarantee for the rotating world
Chuck-type fixtures are mainly used in rotating processing equipment such as lathes. It can firmly clamp the workpiece to keep it stable during high-speed rotation. Common ones are three-jaw chucks and four-jaw chucks. The three-jaw chuck uses the synchronous movement of three jaws to center and clamp the circular workpiece. Its advantages are high automatic centering accuracy and fast clamping of the workpiece. It is suitable for the processing of round bars or disc parts in mass production. Each jaw of the four-jaw chuck can be adjusted independently, which enables it to clamp irregularly shaped or eccentric workpieces, but it takes more time to align and adjust when in use.
3. Vise-type clamp: a powerful assistant for machining
Vise-type clamps are classic in machining workshops. It is generally composed of a fixed clamp body, a movable clamp body, a screw and other components. By rotating the screw, the movable clamp body can move along the guide rail to achieve the clamping and loosening of the workpiece. Vise-type clamps can provide a large clamping force and are suitable for a variety of machining operations such as milling and benchwork. For example, when milling a plane, fixing the workpiece on the vise can ensure that the workpiece will not be displaced during the machining process, thereby obtaining a high-precision machining surface. In addition, some vises are also equipped with a rotatable base to facilitate machining operations at different angles.
4. Magnetic clamps: invisible power
Magnetic clamps use magnetic force to clamp the workpiece, which is a non-contact clamping method. Its working principle is based on electromagnetic induction or the magnetism of permanent magnets. In the electronics manufacturing industry, magnetic clamps are widely used in the assembly and welding of circuit boards. Since it does not require mechanical contact, it will not damage the surface of the workpiece, and the clamping and loosening operations are very fast, which can effectively improve production efficiency. In addition, in some precision processing fields, such as grinding and polishing of optical lenses, magnetic clamps can ensure that the lenses will not be deformed due to external forces during processing, thereby ensuring processing accuracy.
5. Vacuum clamps: the magical charm of adsorption
The vacuum clamp forms a negative pressure between the workpiece and the clamp by vacuuming, thereby clamping the workpiece. This clamp is particularly suitable for clamping workpieces with smooth surfaces and complex shapes, such as glass and plastic plates. In the glass processing industry, vacuum clamps can firmly adsorb glass for cutting, drilling and other processing operations. Its advantage is that the clamping force is evenly distributed, it will not cause local stress concentration on the workpiece, and it can adapt to workpieces of different shapes and sizes. At the same time, the loading and unloading process of the vacuum clamp is also very fast, which can greatly shorten the production cycle.
There are many types of clamps, each with its unique working principle, applicable scenarios and advantages. Whether in large-scale industrial production lines or in small handicraft workshops, the correct selection and use of fixtures can significantly improve work efficiency and processing quality. With the continuous advancement of science and technology, the design and manufacture of fixtures are also constantly innovating. In the future, we are expected to see more powerful and intelligent fixtures appear, injecting new vitality into the development of various industries.
These are just a few of the factors involved in selecting the right clamp. Contact us for more information on finding the perfect clamp type for your application.