Spring Hose Clamps: A Comprehensive Overview
1.What are Spring Hose Clamps? The spring hose clamp is a common connector for fastening hoses, mainly composed of a…
1.What are Spring Hose Clamps?
The spring hose clamp is a common connector for fastening hoses, mainly composed of a spring and a metal clamp body. It uses the elastic tension of the spring to firmly clamp the hose to the pipe or pipeline to prevent loosening and leakage between the hose and the pipe. Its working principle is based on the elastic deformation of the spring. When the spring hose clamp is installed on the hose and pipe, the spring is compressed, generating a continuous contraction force, tightly clamping the hose, so that the hose and the pipe fit tightly, thereby achieving the dual functions of sealing and fixing.

2.What types of spring hose clamps are there?
Common spring hose clamps mainly include worm-type spring hose clamps and double-wire spring hose clamps. The worm-type spring hose clamp adjusts the tightness of the spring by rotating the worm, and can be flexibly adjusted according to different pipe diameters and sealing requirements. It has a wide range of applications and is widely used in automotive cooling systems, industrial pipelines and other fields; the double-wire spring hose clamp consists of two steel wires and a spring. It has a simple and compact structure and good sealing. It is often used in fuel lines, brake systems and other occasions with high sealing requirements, and has obvious advantages in installation environments with limited space.
3.What are the main performance advantages of spring hose clamps?
The biggest advantage of the spring hose clamp is its good sealing and adaptability. Since the spring always maintains a certain tension, even when the hose expands or contracts slightly due to temperature changes, the spring hose clamp can automatically adjust the clamping force to maintain the sealing effect and effectively prevent the leakage of the medium. At the same time, it has a high fastening strength and can withstand a certain amount of pressure and vibration. In a working environment with large vibration such as automobiles and machinery, it can still ensure the stability of the hose connection and reduce the risk of failure caused by loose connection. In addition, the installation and removal of the spring hose clamp is relatively simple and can be reused, which reduces the maintenance cost.

4.What fields are spring hose clamps suitable for?
In the field of automobile manufacturing, spring hose clamps are widely used in engine cooling systems, fuel supply systems, braking systems, and air conditioning systems, etc., to ensure the reliability and sealing of various pipeline connections and to ensure the normal operation of automobiles; in the industrial field, it is suitable for pipeline connections in the chemical, food, pharmaceutical and other industries. For example, in chemical production, it is used to connect hoses that transport corrosive or high-temperature media to ensure that the media does not leak and prevent safety accidents; in the field of home and construction, spring hose clamps can be used for the connection of water and heating pipes, gas pipes, etc., such as the connection of drain pipes under kitchen sinks, the fixing of water pipes of water heaters, etc., to ensure the safety of household water and gas use.
5.How to choose the right spring hose clamp?
When choosing a spring hose clamp, first determine the specifications of the clamp according to the outer diameter of the hose to ensure that the clamp can fit the hose tightly. Secondly, consider the working environment and medium characteristics. If it is used in a high-temperature environment, choose a spring hose clamp made of high-temperature resistant material; if it is conveying corrosive media, choose a clamp with anti-corrosion properties. In addition, pay attention to the pressure requirements of the system. For high-pressure systems, choose a spring hose clamp with high fastening strength and good sealing. At the same time, choose a clamp of the appropriate structure type according to the size of the installation space. For example, when the space is narrow, a double-wire spring hose clamp may be more suitable.
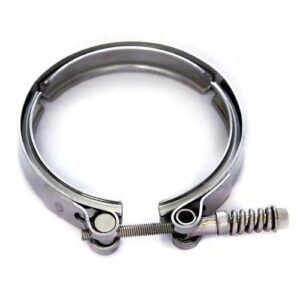
6.What are the installation steps of spring hose clamps?
Before installation, check whether the surface of the hose and pipe fittings is clean and free of debris. Put the spring hose clamp on the hose, and then put the hose on the pipe fitting accurately to ensure that the connection position of the hose and the pipe fitting is correct. Then, use special tools (such as screwdrivers, pliers, etc.) to adjust the tightness of the spring hose clamp. For worm-type spring hose clamps, gradually tighten the clamp by rotating the worm until the appropriate tightness is reached; for double-wire spring hose clamps, use pliers to properly adjust the position of the wire and the tension of the spring. After installation, check whether the clamp is installed in place, whether the connection between the hose and the pipe fitting is firm, and whether there is any leakage.
7.What should I pay attention to when using spring hose clamps?
Avoid over-tightening the spring hose clamp to prevent deformation and damage of the hose due to excessive clamping force, which will affect its service life and sealing performance. During installation and removal, use appropriate tools to avoid scratches or other damage to the clamp and hose. At the same time, regularly check the working status of the spring hose clamp to see if the spring is fatigued or broken, and whether the clamp is loose. If any problems are found, replace or adjust them in time. In addition, spring hose clamps of different materials are suitable for different media and environments. It is strictly forbidden to use them beyond the scope to avoid safety accidents.

8.How to maintain the spring hose clamp?
Regularly clean the dirt, dust and corrosive substances on the surface of the spring hose clamp, keep its surface clean and dry, and prevent the accumulation of dirt from corroding the clamp or affecting the clamping effect. For spring hose clamps that are in harsh environments (such as high temperature, high humidity, and corrosive gas environments) for a long time, the inspection cycle should be shortened to promptly identify potential problems and deal with them. When the elasticity of the spring is weakened or the clamp is obviously worn, replace it with a new spring hose clamp in time to ensure the reliability and sealing of the connection.
9.How do spring hose clamps differ from other types of hose clamps?
Compared with ordinary hose clamps, spring hose clamps do not need to manually adjust the threads to control the tightness. They can automatically adapt to the changes of the hose with the elasticity of the spring, making the operation easier and the sealing performance more stable in dynamic environments. Compared with snap-on hose clamps, spring hose clamps have more uniform tightening force and will not damage the hose due to excessive local force. They are also applicable to a wider range of pipe diameters and have stronger adjustability. In addition, compared with some disposable hose clamps, spring hose clamps are reusable and more economical.
10. What is the future development trend of spring hose clamps?
With the continuous advancement of industrial technology, spring hose clamps will develop in a more efficient and intelligent direction. In terms of materials, R&D personnel will focus on developing new materials with better performance, such as high-strength, high-temperature resistant, corrosion-resistant and lightweight materials, to meet the needs of increasingly complex working conditions. In terms of structural design, there may be more innovative structures with special functions, such as smart spring hose clamps with integrated pressure sensors, which can monitor the pressure changes in the connection parts in real time and warn of leakage risks in advance. At the same time, with the improvement of environmental protection requirements, the production of spring hose clamps will also pay more attention to environmental protection, adopt green production processes and recyclable materials, and reduce the impact on the environment.