Stainless Hose Clamp: Ensuring Reliability and Durability in Hose Connections
In the world of fluid management, hoses are a critical component used to transport various substances, from water to chemicals…
In the world of fluid management, hoses are a critical component used to transport various substances, from water to chemicals and gases. Ensuring that these hoses are securely and reliably connected is essential for preventing leaks and maintaining the integrity of the system. One of the most effective ways to achieve this is through the use of stainless hose clamps. This article delves into the importance of stainless hose clamps, their features, applications, and benefits.
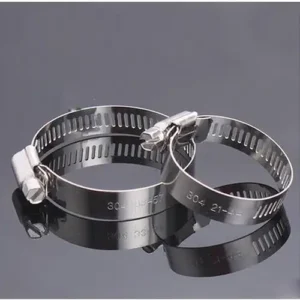
What Are Stainless Hose Clamps?
Stainless hose clamps, also known as stainless steel hose clamps, are fastening devices used to secure hoses to fittings or other components. They are typically made from stainless steel, which provides a high level of strength and resistance to corrosion. These clamps are designed to withstand a wide range of temperatures and pressures, making them suitable for various industrial applications.
Features of Stainless Hose Clamps
Corrosion Resistance: The primary feature of stainless steel clamps is their resistance to corrosion. This makes them ideal for use in environments where exposure to moisture, chemicals, or other corrosive substances is common.
Durability: Stainless steel is known for its durability and long service life. Hose clamps made from this material can endure heavy use and maintain their integrity over time.
Temperature Tolerance: Stainless steel can withstand high temperatures, making these clamps suitable for applications involving hot fluids or in environments with extreme temperature fluctuations.
Strength: The strength of stainless steel ensures that the clamps can handle high pressure without deforming or breaking.
Versatility: Stainless hose clamps come in various sizes and designs to accommodate different hose sizes and types, providing a versatile solution for various applications.
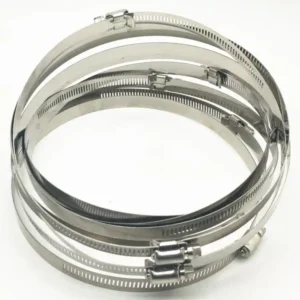
Applications of Stainless Hose Clamps
Stainless hose clamps find use in a wide range of industries due to their robustness and reliability. Some of the common applications include:
Automotive Industry: In vehicles, hoses are used for fuel, coolant, and air intake systems. Stainless clamps ensure these hoses stay securely in place under the hood.
Marine Applications: Boats and ships require hose clamps that can resist saltwater corrosion, making stainless steel an ideal choice.
Food and Beverage Industry: In food processing plants, stainless steel clamps are used to secure hoses that handle food-grade fluids to maintain hygiene and prevent contamination.
Chemical Processing: For the transportation of chemicals, stainless steel clamps provide the necessary strength and resistance to chemical reactions.
Medical Equipment: In medical devices that require fluid transfer, stainless steel clamps ensure secure and leak-free connections.
Benefits of Using Stainless Hose Clamps
Leak Prevention: A secure connection is crucial in preventing fluid leaks, which can lead to equipment damage, environmental pollution, and safety hazards.
Cost-Effective: While the initial cost may be higher than some alternatives, the long-term savings from reduced maintenance and replacement make stainless steel clamps a cost-effective choice.
Safety: The reliability of stainless steel clamps contributes to a safer working environment by reducing the risk of hose failure.
Ease of Installation: Many stainless hose clamps are designed for easy installation, requiring minimal tools and effort.
Aesthetic Appeal: The sleek look of stainless steel can be an advantage in applications where appearance is a consideration.
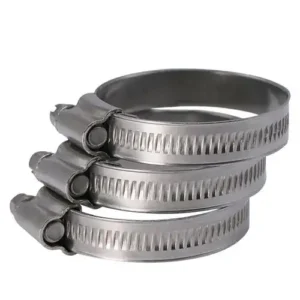
Final Conclusion
Stainless hose clamps are an essential component in maintaining the efficiency and safety of fluid transfer systems. Their corrosion resistance, durability, and versatility make them a preferred choice in many industries. By understanding the features and benefits of stainless hose clamps, engineers and technicians can make informed decisions when selecting the right clamps for their specific applications. As technology advances, the development of even more robust and efficient hose clamps will continue, ensuring that fluid management systems remain reliable and secure for years to come.
Problems encountered and solutions
Installation Problems
Problem: The hose clamp is difficult to align or tighten during installation, making the installation process time-consuming and laborious.
Solution: Choose the appropriate tool, such as a screwdriver or torque wrench, and make sure the tool matches the specifications of the hose clamp. Before installation, the hose and connector can be cleaned and lubricated to reduce friction and facilitate the installation and tightening of the hose clamp.
Sealing problem
Problem: After the hose clamp is installed, there is still leakage at the connection, which affects the normal operation of the system.
Solution: Check whether the surface of the hose and the connector is flat and smooth. If there are impurities or burrs, they need to be cleaned and polished. Ensure that the hose clamp is installed in the correct position and the tightening force is uniform and moderate to avoid being too loose or too tight. Sealant or sealing gasket can be used at the connection between the hose and the connector to enhance the sealing effect.
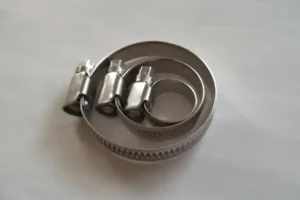
Corrosion Problem
Problem: In harsh working environments, stainless steel hose clamps may corrode, reducing their service life and reliability.
Solution: Depending on the degree of corrosiveness of the working environment, choose stainless steel hose clamps with appropriate materials and protection levels, such as 304 or 316 stainless steel. Regularly inspect and maintain hose clamps to detect and address signs of corrosion in a timely manner. Corroded hose clamps should be replaced in a timely manner to prevent the problem from further deteriorating.
Loosening due to vibration
Problem: The vibration generated during the operation of the equipment may gradually loosen the hose clamp, thus affecting the reliability of the hose connection.
Solution: When installing the hose clamp, you can use anti-loosening devices such as spring washers, nylon nuts, etc. to improve the anti-loosening performance of the hose clamp. Check and deal with the vibration source of the equipment, such as adjusting the balance of the equipment, installing shock-absorbing devices, etc., to reduce the impact of vibration on the hose clamp. Check the tightness of the hose clamp regularly and tighten it in time if it is found to be loose.
Hose clamp selection problem
Problem: If the hose clamp is not selected properly, it may cause the hose clamp to fail to meet the actual working requirements, such as insufficient clamping force, inappropriate size, etc.
Solution: According to the material, outer diameter, working pressure and other parameters of the hose, select the appropriate specification and model of stainless steel hose clamp. When selecting, you can refer to the product catalog and technical specification table of the hose clamp manufacturer, or consult professional technicians for advice.
Maintenance and replacement issues
Problem: Stainless steel hose clamps may experience fatigue, deformation and other problems after long-term use, and need to be maintained and replaced in time, but users may not know when and how to perform maintenance and replacement.
Solution: Establish a regular maintenance system and conduct regular inspections of stainless steel hose clamps, including appearance inspections, tightness inspections, etc. According to the use of hose clamps and working environment, formulate a reasonable replacement cycle, and replace hose clamps that have reached their service life or have serious problems in time.