T-bolt and worm drive clamps differences to match application
In the field of industrial manufacturing, fixtures, as important tools for fixing and positioning workpieces, play a key role in…
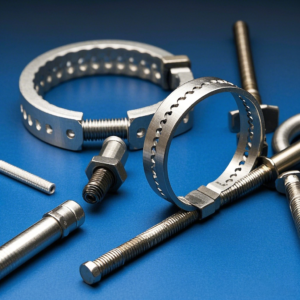
In the field of industrial manufacturing, fixtures, as important tools for fixing and positioning workpieces, play a key role in production efficiency and product quality. T-bolt fixtures and worm drive fixtures are two common types, which have many differences in structure, principle, performance and applicable scenarios. A deep understanding of these differences will help practitioners choose the most suitable fixture for a specific application and improve production efficiency.
Structure and working principle
T-bolt fixture
The T-bolt is named because its shape resembles the letter “T”. It is usually used in conjunction with a T-slot. In a T-bolt fixture, the T-bolt passes through the mounting hole of the fixed part and is embedded in the T-slot. By tightening the nut, the T-bolt generates a lateral tension in the slot, which tightly fixes the workpiece to the workbench or support surface. This fixture has a simple structure, is easy to install and disassemble, and has low technical requirements for workers. For example, on a milling machine for machining, T-bolts are often used to fix tooling fixtures or workpieces to ensure stability during processing.
Worm drive fixture
The worm drive fixture consists of a worm, a worm wheel and a clamp arm. When the worm is turned, the worm drives the worm wheel to rotate, which in turn causes the clamp arm to open and close, thereby clamping and loosening the workpiece. The worm has a self-locking characteristic, that is, the reverse force cannot rotate the worm, which ensures the high stability of the fixture in the clamped state. In the welding workshop of automobile manufacturing, the positioning and clamping of many parts rely on worm drive fixtures to ensure welding accuracy and quality.
Performance characteristics comparison
Clamping force and precision
The clamping force of the T-bolt fixture mainly depends on the tightening degree of the nut. Generally speaking, its clamping force is relatively limited. Due to the large influence of human factors during operation, it is difficult to achieve high-precision clamping and positioning. In some rough processing occasions where precision is not required, such as wood cutting and drilling of simple metal parts, the T-bolt fixture can meet basic needs.
In contrast, the worm drive fixture can generate a larger clamping force by reasonably designing the transmission ratio of the worm wheel. At the same time, its self-locking characteristics and precise mechanical structure make the clamping accuracy higher and the repeated positioning error smaller. In industries with extremely high precision requirements such as electronic equipment manufacturing, worm drive clamps can ensure the position accuracy of tiny parts during processing and improve product yield.
Operational convenience
The operation of T-bolt clamps is relatively simple. Workers only need to tighten or loosen the nuts with a wrench to complete the clamping and disassembly work, without the need for complex tools and skills. However, in situations where workpieces need to be replaced frequently, each installation and removal of T-bolts takes a certain amount of time, affecting production efficiency.
The operation of worm drive clamps is relatively convenient. By turning the worm, the clamp arm can be quickly opened and closed, greatly shortening the clamping time. Some advanced worm drive clamps are also equipped with a quick adjustment device to further improve the operating efficiency. They are suitable for scenes with high production rhythm requirements such as assembly line operations.
Application scenario selection
Applicable scenarios of T-bolt clamps
Due to their simple structure and low cost, T-bolt clamps are widely used in situations where precision requirements are not high and the working environment is relatively harsh. In construction, the fixtures used to fix scaffolding and formwork mostly use T-bolt structures to adapt to complex outdoor working conditions and larger workpiece sizes. In addition, in some small mechanical processing plants, T-bolt fixtures are also a common choice for fixing basic tooling and workpieces.
Applicable scenarios for worm drive fixtures
For processing tasks requiring high precision and high stability, worm drive fixtures are an ideal choice. In the aerospace field, the processing accuracy of parts is directly related to the performance and safety of aircraft. Worm drive fixtures can meet the precise clamping requirements for complex-shaped parts. On automated production lines, the fast clamping characteristics of worm drive fixtures also help improve production efficiency and realize automation and intelligence of the production process.
T-bolt fixtures and worm drive fixtures each have their own advantages and disadvantages, and play a unique role in different application scenarios. Only by fully understanding their structure, principle and performance differences, combined with specific production needs, can we make the right choice and create greater value for the enterprise.