Windshiled Pump Hose Clamp: A Comprehensive Overview
The windshiled pump hose clamp is a critical component in various industrial and automotive applications, ensuring the secure and efficient…
The windshiled pump hose clamp is a critical component in various industrial and automotive applications, ensuring the secure and efficient transfer of fluids. This article delves into the importance of hose clamps, their design, materials, and maintenance, providing a comprehensive understanding of this essential tool.
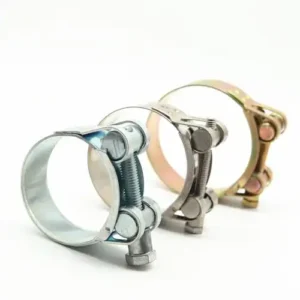
Hose clamps, also known as hose clips or hose clamps, are used to secure hoses to fittings, ensuring a leak-proof connection. In the context of windshiled pumps, these clamps play a vital role in maintaining the integrity of the fluid transfer system. A windshiled pump, often found in automotive applications, requires robust and reliable hose clamps to prevent fluid leaks that could lead to system failure or safety hazards.
Types of Hose Clamps
There are several types of hose clamps, each designed for specific applications:
1.Perpendicular or T-Clamp: These clamps have a T-shaped end, which allows for easy tightening around the hose.
2.Straight or I-Clamp: This type of clamp is straight and is often used in applications where space is limited.
3.Swivel or J-Clamp: These clamps have a swiveling end, providing flexibility and ease of installation.
4.worm gear clamps: These are tightened using a worm gear mechanism, providing a secure and adjustable grip.
Each type has its advantages and is chosen based on the specific requirements of the application, such as the type of hose, the fluid being transferred, and the environmental conditions.
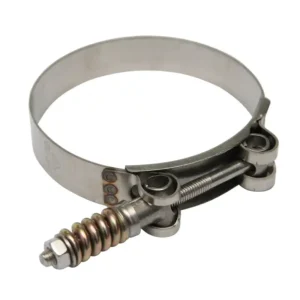
Materials and Construction
Hose clamps are made from a variety of materials to suit different needs:
1.Stainless Steel: Offers excellent corrosion resistance and is suitable for most industrial and automotive applications.
2.Aluminum: Lightweight and corrosion-resistant, making it a popular choice for automotive applications.
3.Plastic: Inexpensive and suitable for non-critical applications where weight is a concern.
4.Viton or Rubber: Used for the band part of the clamp to ensure a secure grip on the hose without causing damage.
The choice of material depends on the chemical compatibility with the fluid being transferred and the environmental conditions the clamp will be exposed to.
Installation and Tightening
Proper installation is crucial for the performance of hose clamps:
1.Select the Right Size: The clamp should be the correct size for the hose to ensure a secure fit without damaging the hose.
2.Position the Clamp: Place the clamp in the correct position on the hose, ensuring it is aligned with the fitting.
3.Tighten the Clamp: Use a suitable tool to tighten the clamp. Over-tightening can damage the hose, while under-tightening can lead to leaks.
It’s important to follow the manufacturer’s guidelines for tightening torque to ensure the clamp is secure without causing damage.
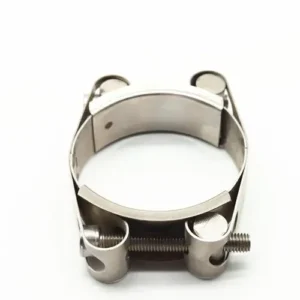
Maintenance and Replacement
Regular maintenance is essential to ensure the longevity and performance of hose clamps:
1.Inspect for Wear: Regularly check the clamp for signs of wear or damage, such as cracks or corrosion.
2.Check for Leaks: Periodically inspect the hose and clamp connection for leaks.
3.Replace as Necessary: If a clamp shows signs of wear or damage, it should be replaced to prevent leaks or system failure.
Proper maintenance can extend the life of the hose and clamp, reducing downtime and costs associated with repairs.
In conclusion, the windshiled pump hose clamp is a critical component in fluid transfer systems. Understanding the different types, materials, and proper installation and maintenance practices is essential for ensuring the efficiency and safety of these systems. By choosing the right clamp for the application and following best practices for installation and maintenance, users can prevent leaks, reduce downtime, and extend the life of their fluid transfer systems.
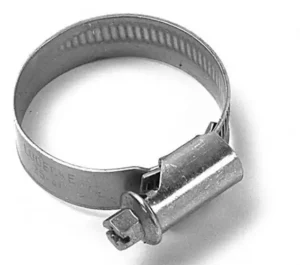
Problems Encountered
1. Leakage at the Hose Connection
One of the most common issues is the occurrence of leaks where the hose attaches to the pump. This can be due to improper installation of the hose clamp, such as not tightening it enough. Over time, the vibration and movement of the pump can cause the hose to shift slightly, leading to a gap where the fluid can escape.
Another factor could be the degradation of the hose material. If the hose has become brittle or cracked, it won’t form a proper seal even with a correctly installed clamp.
2. Clamp Corrosion
In certain environments, especially those with high humidity or exposure to chemicals, the hose clamp can corrode. Corrosion weakens the structural integrity of the clamp, making it less effective at holding the hose firmly in place. This can also lead to difficulties in loosening or tightening the clamp when maintenance is required.
3. Incorrect Clamp Sizing
Selecting a hose clamp that is either too small or too large for the hose diameter can cause problems. A clamp that is too small may not fit properly around the hose, leading to uneven pressure distribution and potential damage to the hose. On the other hand, a clamp that is too large won’t be able to provide sufficient clamping force, resulting in a loose connection and possible leakage.
Solutions
1. Proper Installation and Tightening
When installing the hose clamp, ensure that it is centered correctly over the hose and the connection point. Use a torque wrench to tighten the clamp to the manufacturer’s recommended specifications. This will ensure a consistent and proper seal without over-tightening, which could damage the hose.
Regularly check the tightness of the clamp, especially after the pump has been in operation for some time or if there has been any significant vibration or movement.
2. Corrosion Prevention and Treatment
For environments where corrosion is a concern, choose hose clamps made from corrosion-resistant materials such as stainless steel. If corrosion has already occurred, remove the clamp and clean it using a suitable rust remover. Apply a protective coating, such as a rust inhibitor or paint, to prevent further corrosion. In severe cases, it may be necessary to replace the clamp entirely.
3. Correct Clamp Sizing
Always measure the hose diameter accurately before selecting a hose clamp. Refer to the manufacturer’s sizing charts to ensure the proper fit. If in doubt, it is better to choose a slightly larger clamp and use a spacer or gasket to adjust the fit rather than using a clamp that is too small.