Worm Drive Fuel Line Hose Clamps: A Comprehensive Overview
Fuel line hose clamps are critical components in automotive and industrial settings, ensuring secure and leak-proof connections in fuel systems….
Fuel line hose clamps are critical components in automotive and industrial settings, ensuring secure and leak-proof connections in fuel systems. Among various types of hose clamps, worm drive hose clamps stand out for their strength and adjustability. This article delves into the importance, functionality, and application of worm drive fuel line hose clamps.
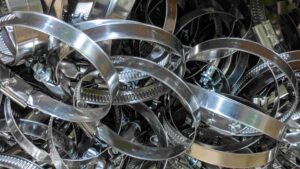
What Are Worm Drive Fuel Line Hose Clamps?
Worm drive hose clamps, also known as worm gear clamps, are mechanical devices designed to secure and seal hoses onto fittings or connectors. They are particularly important in fuel systems, where they maintain the integrity of fuel line connections, preventing leaks and ensuring fuel is delivered securely from the tank to the engine.
These clamps work by applying consistent pressure around the hose’s circumference, compressing it against the fitting to form a secure seal. They consist of a stainless steel band with a screw mechanism (the “worm gear”) that tightens the band around the hose. As the screw is turned, the band tightens, compressing the hose around the fitting.
Applications and Strengths
Worm drive clamps are suitable for a wide range of applications, including automotive fuel lines, coolant hoses, and air hoses. They are popular due to their versatility and ease of adjustment. The primary strengths of worm drive clamps include a strong and adjustable grip, ease of installation and removal, and wide availability. However, they may not provide an even seal if not installed correctly and have the potential for over-tightening, which can damage the hose.
Importance of Proper Fit and Compatibility
The clamp should fit snugly around the hose without cutting into the material. Over-tightening a clamp can damage the hose, while a loose clamp may not hold the hose securely, leading to potential leaks. It’s also crucial to choose a hose clamp compatible with the specific type of fuel being used. Stainless steel clamps are recommended for ethanol and other alternative fuels that can be more corrosive than traditional gasoline or diesel.

Installation Techniques
Proper installation of worm drive hose clamps on fuel lines is essential for a secure connection that prevents leaks and maintains the integrity of the fuel system. Here’s a step-by-step guide to installing these clamps effectively:
1.Inspect the Hose and Fitting: Before installation, check for wear, damage, or contamination, ensuring the hose is free from cracks and the fitting is clean and smooth.
2.Select the Right Hose Clamp: Choose a clamp that fits your hose and fitting correctly, able to tighten securely without being overextended.
3.Positioning the Hose: Slide the clamp onto the hose before attaching it to the fitting, positioning it close to the end but not too close to avoid pinching.
4.Attach the Hose to the Fitting: Push the hose fully onto the fitting, ensuring it is seated properly and there are no gaps or twists.
5.Positioning the Clamp: Place the hose clamp over the fitting’s barb or the area where the hose is most securely seated, centering it over the barb for the most secure grip.
6.Tighten Evenly: Using the appropriate tool, begin tightening the clamp slowly, ensuring it tightens evenly around the hose. Tighten until the hose is securely compressed against the fitting but avoid over-tightening.
7.Check for a Secure Fit: Once tightened, check that the clamp is secure and the hose does not slip off the fitting when gently tugged. There should be no gaps between the hose and the fitting, and the clamp should not be excessively tight.
Market Insights
The global market for hose clamps, including worm drive fuel line hose clamps, has witnessed steady growth due to increasing demand for reliable and efficient hose connections across multiple industries. The automotive sector is a major consumer of hose clamps, and the market is shifting towards lightweight and corrosion-resistant materials, improving performance and durability. Technological advancements, such as smart clamps with integrated sensors, are opening new avenues in the market.
In conclusion, worm drive fuel line hose clamps are essential for maintaining the safety and efficiency of fuel systems in vehicles. Proper selection, installation, and maintenance are crucial to prevent leaks and ensure the longevity of the fuel system components.
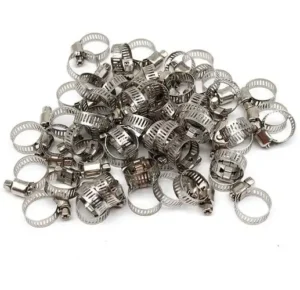
Problems and Solutions
Worm drive fuel line hose clamps, while essential for maintaining the integrity of fuel systems, are not without their challenges. Understanding these issues and their corresponding solutions is crucial for ensuring optimal performance and safety.
1.Problem: Corrosion
In environments where fuel line hose clamps are exposed to moisture, chemicals, or harsh weather conditions, corrosion can set in. This is particularly problematic in marine applications or in regions with high humidity. Corroded clamps lose their structural integrity, leading to weakened clamping force and potential fuel leaks.
Solution: Opt for hose clamps made from corrosion-resistant materials such as stainless steel or aluminum alloys. Additionally, applying anti-corrosion coatings can provide an extra layer of protection. Regular inspection and maintenance schedules should be implemented to detect and address any signs of corrosion early on.
2.Problem: Incorrect Installation
Improper installation is a common culprit behind hose clamp failures. Over-tightening can damage the hose, causing cracks or deformations that compromise its ability to contain fuel. Under-tightening, on the other hand, fails to create a proper seal, resulting in leaks.
Solution: Follow the manufacturer’s recommended torque specifications during installation. Use calibrated tools to ensure accurate tightening. Training technicians on proper installation techniques and providing detailed installation guides can significantly reduce errors.
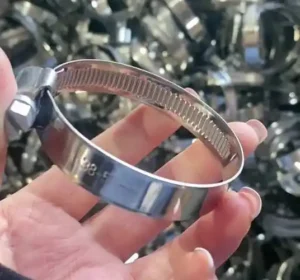
3.Problem: Vibration-Induced Loosening
In applications where the fuel system is subject to continuous vibrations, such as in engines, worm drive hose clamps may gradually loosen over time. This can lead to fuel seepage and a loss of system efficiency.
Solution: Consider using clamps with self-locking or vibration-resistant features. These may include lock washers, nylon inserts, or specialized locking mechanisms that prevent the screw from backing out due to vibrations. Periodic re-tightening checks during routine maintenance can also catch and correct any loosening before it becomes a major issue.
4.Problem: Compatibility with Hoses
Not all hose clamps are suitable for every type of fuel hose. Using the wrong clamp size or style can result in an ineffective seal or damage to the hose.
Solution: Ensure proper compatibility by referring to the hose and clamp manufacturers’ specifications. Select clamps that match the hose’s diameter, material, and pressure rating. Conduct compatibility tests during the design and prototyping stages of a fuel system to avoid issues in the field.
By proactively addressing these common problems and implementing the appropriate solutions, the reliability and performance of worm drive fuel line hose clamps can be maximized, safeguarding the integrity of fuel systems across various industries.